Recent years have been marked by an exceptional phenomenon, in the form of the Covid-19 pandemic. As a player in the healthcare sector, IVIDATA Life Sciences had a role to play. Our teams worked alongside some of the major stakeholders in the field, particularly on vaccine production. For example, Mahdi, a quality assurance consultant at IVIDATA Life Sciences, worked on vaccine production for 9 months with a supplier of research and analysis equipment for laboratories. He talks to us about his mission, the issues involved, and the role he played.
Quality assurance: a major challenge in vaccine production
The company we work with produces the vaccine’s active substance, which is injected into the patient. This is the raw material that is then passed on to other industries whose role is to dilute the product in syringes or vials.
Our expert joined the project in 2021 as a quality assurance consultant. He was involved in the quality review of batch records. This involved checking that the information and data complied with the procedures and with what was indicated in the documentation. He made sure that there were no anomalies or deviations, and was then in charge of quality approval.
If any deviations were found, his role was to monitor how they were dealt with, to understand the source of the problem and its impact, and to analyse whether this had affected the quality of the product. For certain deviations, he had to implement preventive and corrective actions to avoid the problem recurring and thus improve procedures.
Once these actions had been completed, the batches could be sent to the Qualified Person (QP, a responsible pharmacist) who releases each batch and is legally responsible for certifying that it has been produced correctly.
A major project in an extraordinary context
The project was launched at the beginning of 2020, at the start of the pandemic, and had to be implemented quickly. It was a very special context, since it was essential to produce continuously to be able to quickly meet the needs of the market and customers, while guaranteeing the quality of the product. The team was under a lot of pressure, as many countries around the world were at a standstill for several months/years, so there was a real sense of expectation. At the same time, ensuring the quality of the project and dealing with any deviations is not optional in our field, as everyone’s health is at stake.
It was a very challenging project, and all the teams had to be autonomous, flexible, and highly responsive in order to quickly find solutions and unblock production.
With this type of project, there are often deviations. These have to be dealt with within a very specific timeframe. The urgency of setting up the project had an impact on the organisation and workload of the teams. Unfortunately, during a period when many deviations were not dealt with in time, the team had to adapt, develop processes, and implement a continuous improvement system, given the health context.
Three keys to improving quality assurance
Our consultant helped to improve the quality process and reduce the number of deviations by taking several actions.
Firstly, by analysing in detail the reasons why certain deviations had occurred. Numerous site visits were carried out to detect any problems in the production areas.
Secondly, good collaboration and communication with the production teams were essential. Several meetings were organised to discuss the various problems faced by each team member in order to implement the necessary actions and reduce the deviations while respecting the interests of all the teams.
Finally, we had to further develop our processes, particularly with regard to data integrity. Until now, the teams cleaned up the data but did not report the actions that had been taken. The team has changed the training matrices for new internal recruits and new contractors to include reporting in the process, and this is communicated to everyone as soon as they join the company. To improve the review of batch records, we also introduced a Badge Record (BR) Assessment. This involves summarising all the events that have occurred, the results, settings, deviations, and CAPAs for each batch in a standardised file, to give the QP a clearer overview of the history.
Contact
us
Discover also
Tailored solutions for your needs
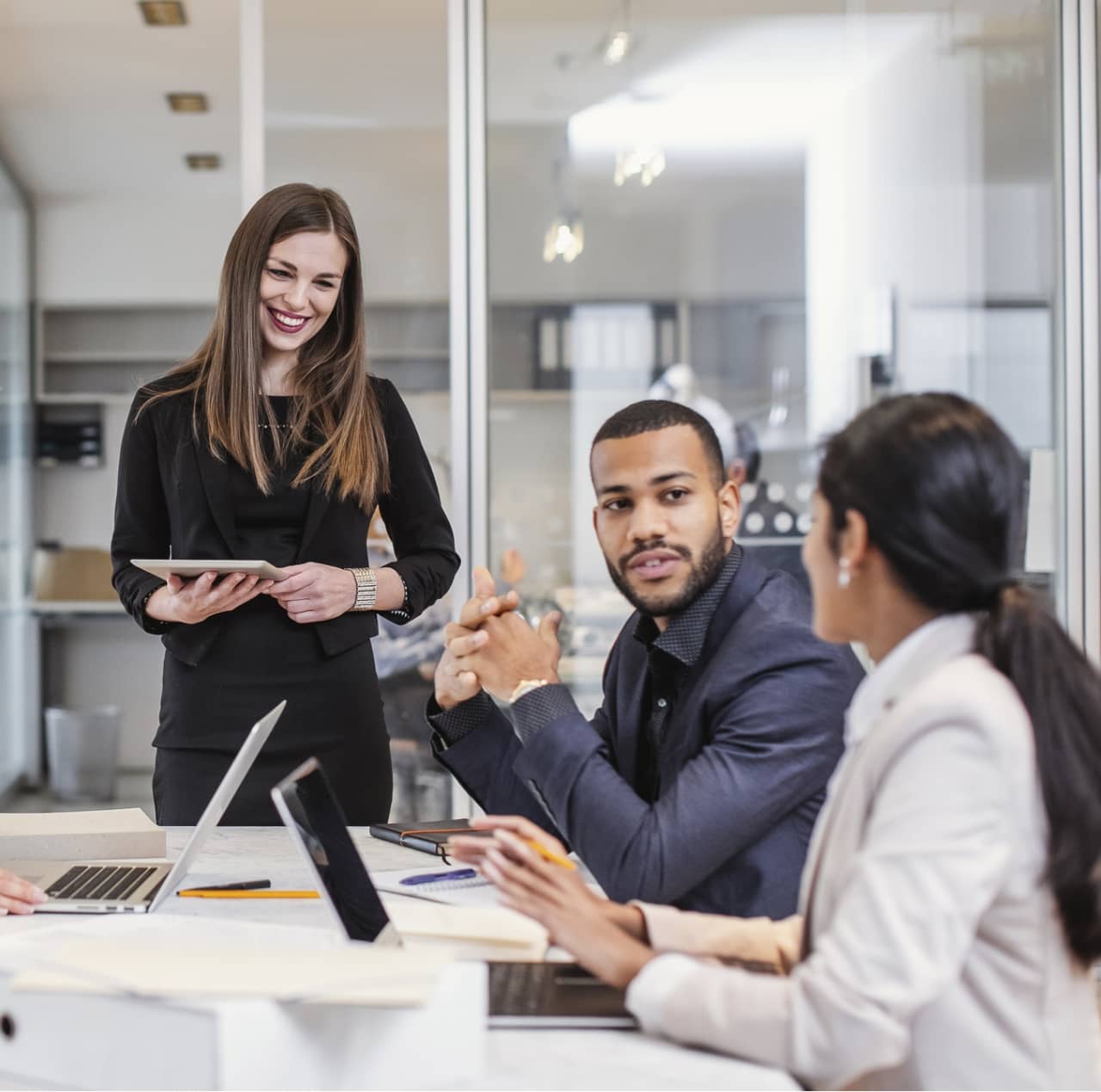
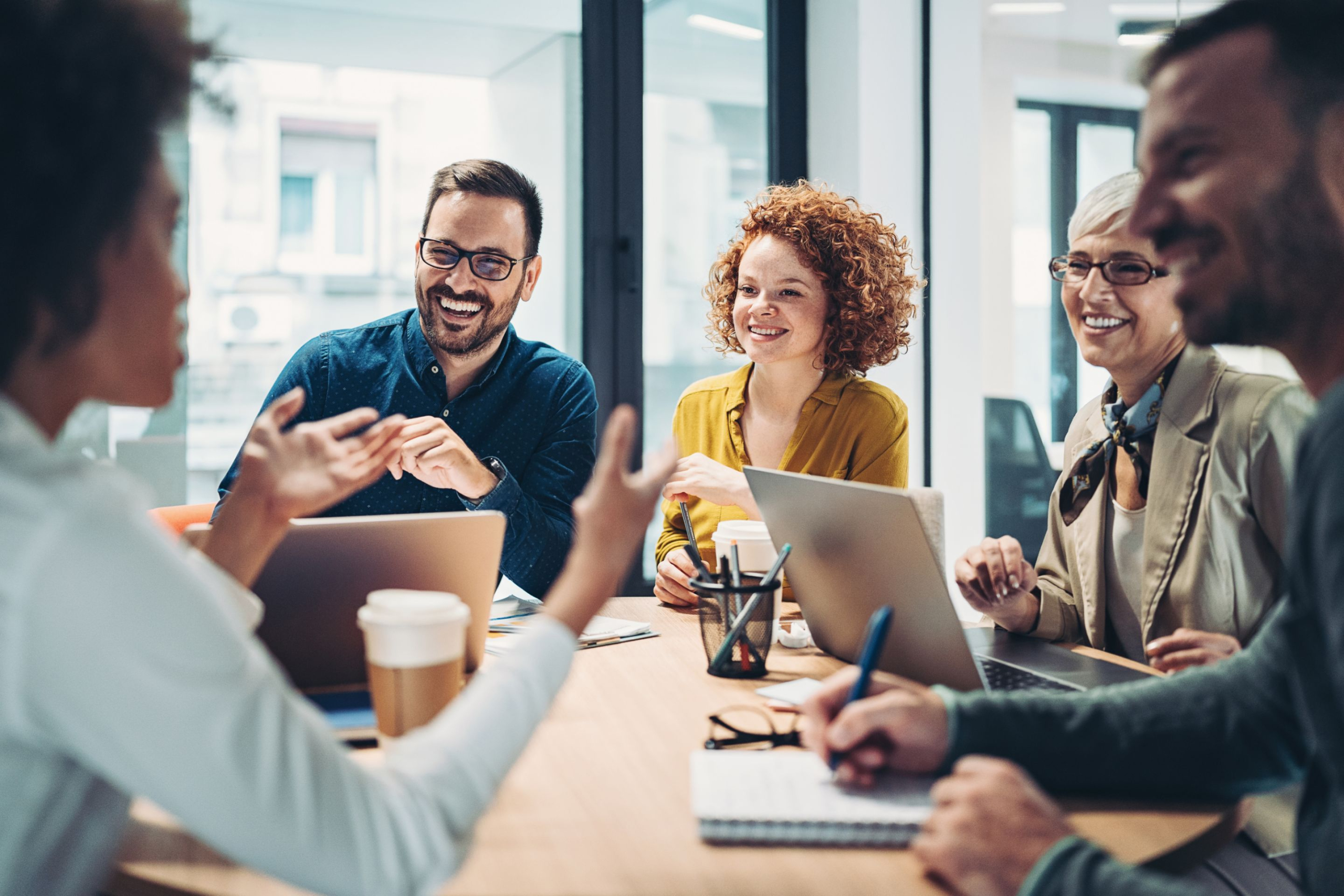
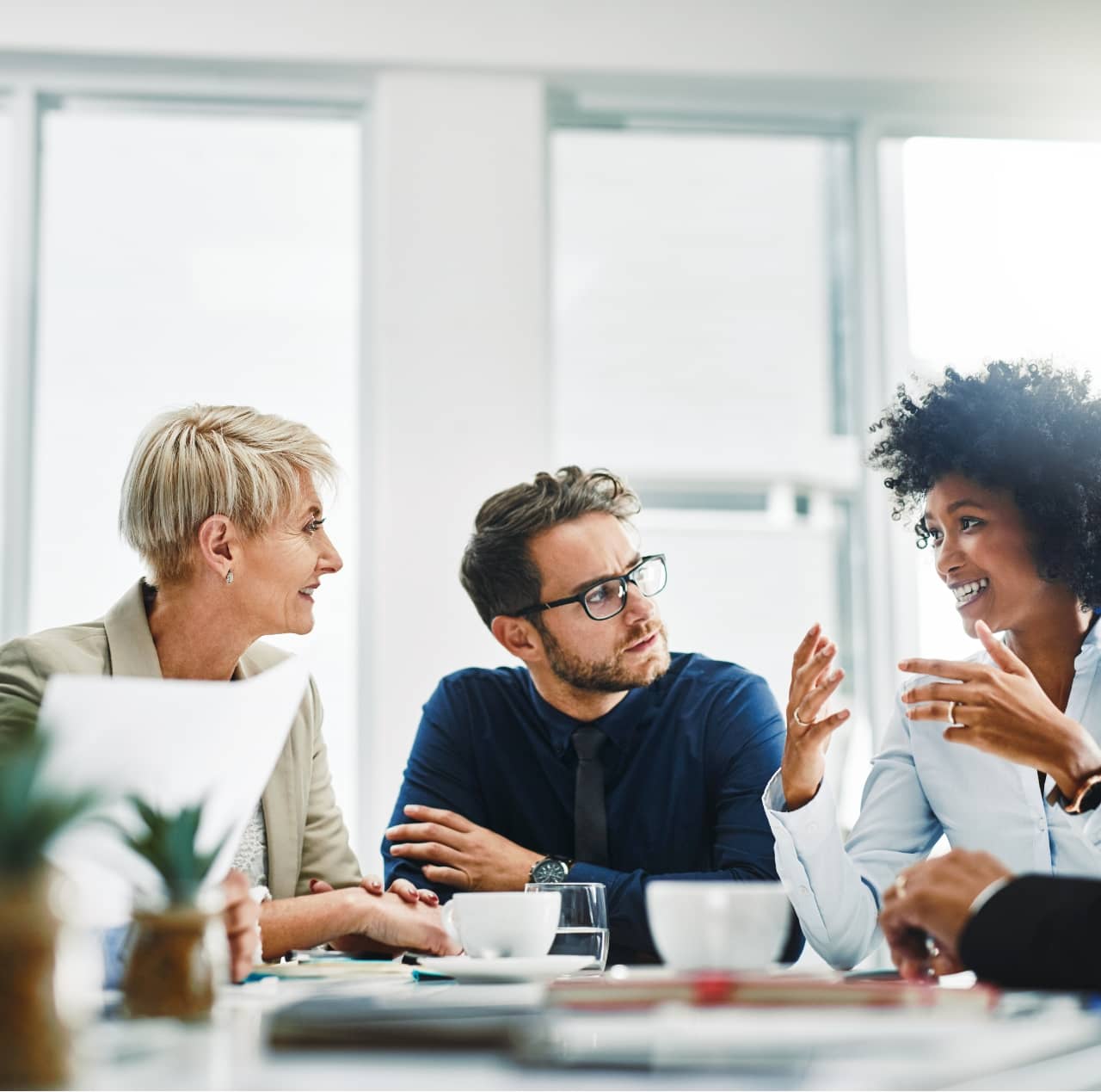